Clean water is a prerequisite for every industrial and household process, and the key to achieving this is by utilizing efficient and effective filtration systems. In this article, we will explore the remarkable realm of Polypropylene or PP Cartridge Filters and PP Filters, demystifying their working principles, application scenarios, and highlighting their considerable advantages.

An Introduction to PP Cartridge Filters and PP Filters
Polypropylene, fondly referred to as PP, is a widely used material in the construction of filter elements due to its high mechanical strength, excellent chemical resistance, and food-grade safety. The PP Cartridge Filter and PP Filter are industry standards for water filtration, recognized for their reliability and durability. Their design encompasses pleated or melt-blown filter media, encased within a rugged polypropylene framework, delivering superior filtration efficacy.

The Versatility in Application Scenarios
The PP Cartridge Filters and PP Filters find extensive application across various sectors, testament to their versatility and effectiveness. They are used in pharmaceuticals, food & beverage production, electronics manufacturing, and petrochemical industries, among others. The robustness of PP filters allows them to handle a wide range of fluid viscosities and temperatures, making them suitable for diverse fluid filtration applications.
A Panoply of Product Advantages
One of the most notable advantages of PP Cartridge Filters and PP Filters is their excellent chemical compatibility. They are resistant to most acids, bases, and solvents, ensuring their longevity in harsh chemical environments. Their pleated design offers a large surface area, promoting high dirt-holding capacity and long service life. In addition, the non-fibre releasing and thermal bonding characteristics of PP Filters ensure their suitability for critical and sterile filtration applications.

Unpacking the Working Principles
The primary working principle of a PP Cartridge Filter and PP Filter is mechanical filtration. This involves the removal of particulate matter from the fluid by directing it through the filter medium. Particles larger than the pore size of the filter medium are captured on its surface or within the filter depth. The pleated construction of the PP Cartridge Filters provides an extended surface area, thereby increasing the volume of fluid that can be filtered before the cartridge needs to be replaced.
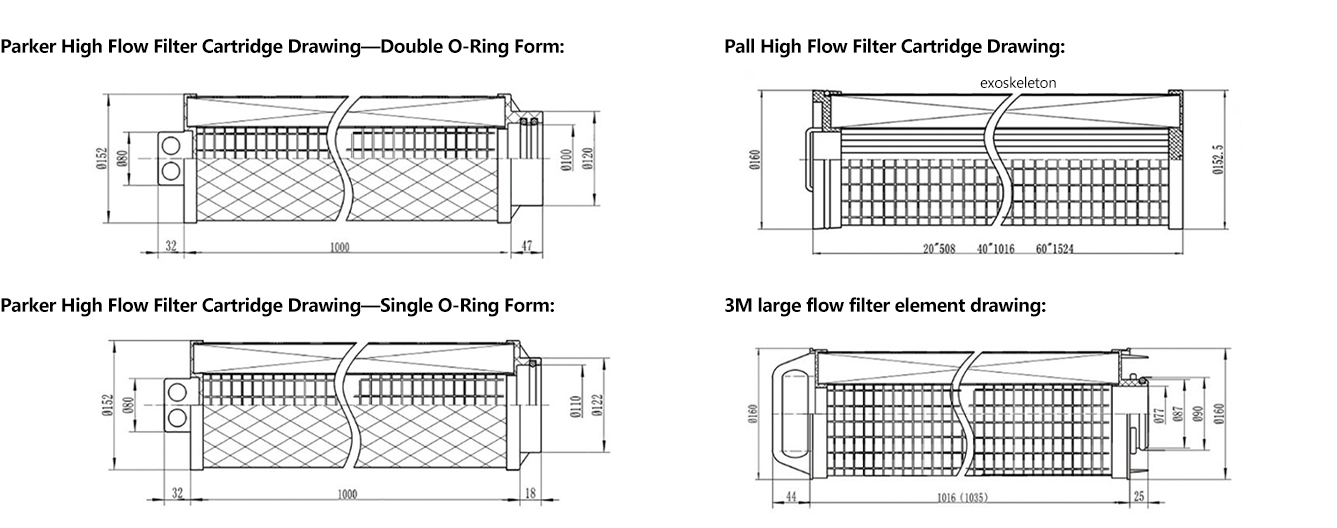
Technical parameters

Specification

PP Cartridge Filters and PP Filters: A Recap
PP Cartridge Filters and PP Filters, crafted from durable, chemically resistant polypropylene, are a staple in various industries ranging from food and beverage to pharmaceuticals and petrochemicals. Renowned for their high mechanical strength, extensive chemical compatibility, and thermal stability, these filters offer reliable and efficient filtration.

Predicted Application Scenarios
While already extensive, the application scenarios for PP Cartridge Filters and PP Filters are expected to grow in the future. Emergent sectors like alternative energy, biotechnology, and advanced materials manufacturing may soon come to rely heavily on these robust filtration systems. The ability of these filters to handle diverse fluid viscosities and temperatures, coupled with their suitability for sterile filtration applications, positions them as invaluable assets in these growing industries.
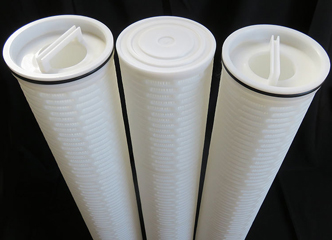
Anticipated Product Advancements
As we look to the future, we envision significant advancements in the design and fabrication of PP Filters. Enhancements in the pleat technology may further increase the surface area of the filters, allowing for even greater dirt-holding capacity. Innovations in the material science sector could lead to the development of new polypropylene alloys or composites, improving the filters' resistance to extreme temperatures and corrosive substances.
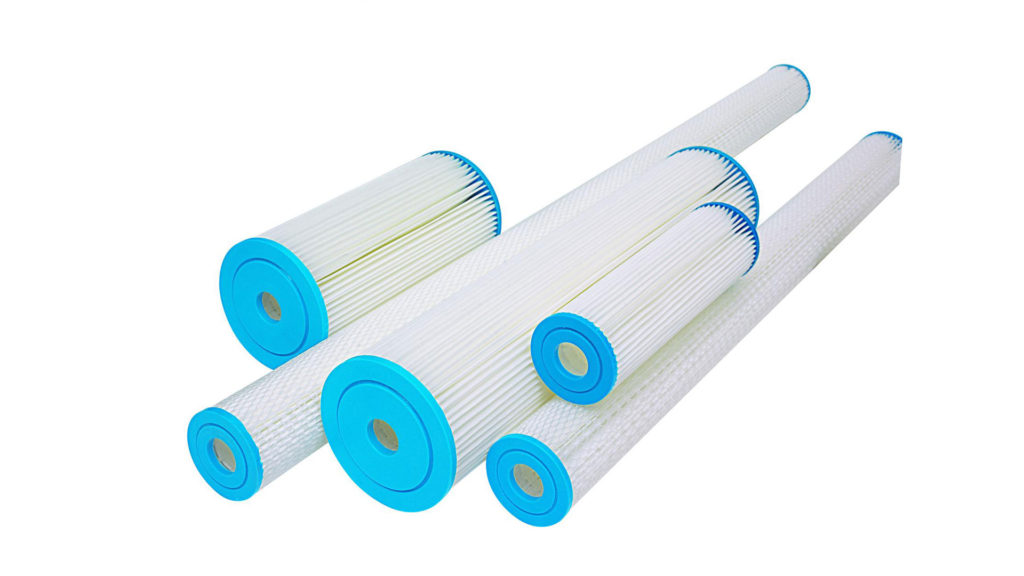
Evolution of Working Principles
The primary working principle of PP Cartridge Filters and PP Filters, mechanical filtration, is unlikely to change in the future. However, technological advancements could augment the efficiency of this process. One possibility is the integration of nanotechnology into the filter medium, which could allow for the filtration of smaller, nano-sized particles without a corresponding decrease in flow rate.
Embracing Sustainability
The future of PP Cartridge Filters and PP Filters also lies in sustainability. Biodegradable or recyclable polypropylene options could soon become viable alternatives to current materials, reducing the environmental impact of discarded filters. Further, energy-efficient manufacturing processes could significantly lower the carbon footprint of these products.
In conclusion, the future of PP Cartridge Filters and PP Filters holds promise. While their inherent properties will continue to make them reliable filtration options, advancements in technology and a commitment to sustainability will ensure that they remain at the forefront of filtration solutions. As we navigate through the future, these filters will continue to evolve, adapting to our ever-changing needs and maintaining their position as vital components of various industries.

FAQ
Q: How are high flow filter elements used in the semiconductor industry?
A: High flow filter elements are used in the semiconductor industry to filter process fluids and gases. They help in maintaining the ultra-clean environments that are critical in semiconductor manufacturing.
Q: What role do high flow filter elements play in power generation?
A: In power generation, high flow filter elements can be used in various applications such as cooling water filtration, fuel oil filtration, and turbine lube oil filtration. They help in maintaining the efficiency and longevity of the equipment.
Q: How are high flow filter elements used in the pharmaceutical industry?
A: High flow filter elements are used in the pharmaceutical industry for applications such as purifying water, filtering process fluids, and ensuring the cleanliness of products. They need to meet stringent quality and safety standards.